揭開神秘面紗:鋰離子電池的超強理論容量
By hoppt
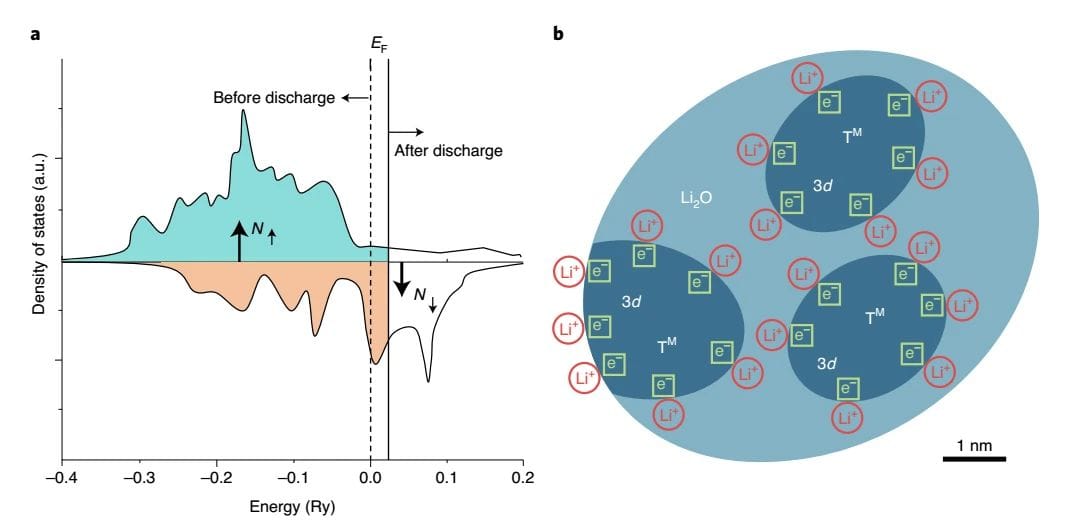
鋰電池為何存在超理論容量現象
在鋰離子電池(LIB)中,許多過渡金屬氧化物基電極表現出異常高的儲存容量,超出了其理論值。 儘管這種現像已被廣泛報道,但這些材料的潛在物理化學機制仍然難以捉摸,並且仍然是一個有爭議的問題。
結果簡介
近日,加拿大滑鐵盧大學苗國興教授、德克薩斯大學奧斯汀分校餘桂華教授以及青島大學李洪森、李強在Nature Materials上聯合發表題為“Extra storage capacity in原位磁力測量揭示的過渡金屬氧化物鋰離子電池」。 在這項工作中,作者利用原位磁監測證明了金屬奈米顆粒上存在強表面電容,並且大量自旋極化電子可以儲存在已經還原的金屬奈米顆粒中,這與空間電荷機制一致。 此外,所揭示的空間電荷機制可以擴展到其他過渡金屬化合物,為建立先進的儲能係統提供關鍵指導。
研究亮點
(1)利用原位磁監測技術研究了典型Fe3O4/鋰電池內部電子結構的演化;
(2)揭示了Fe3O4/Li體系中,表面電荷容量是額外容量的主要來源;
(3)金屬奈米顆粒的表面電容機制可以擴展到廣泛的過渡金屬化合物。
文字及文字引導
- 結構表徵和電化學性能
以常規水熱法合成單分散空心Fe3O4奈米球,然後在100 mAg−1電流密度下進行充放電(圖1a),第一次放電容量為1718 mAh g−1,第二次和第三次放電容量分別為1370 mAhg−1 1,364和1 mAhg−926,遠超過1 mAhg−1的理論預期。 完全放電產物的BF-STEM圖像(圖3b-c)表明,鋰還原後,Fe4O1奈米球轉化為更小的Fe奈米顆粒,尺寸約為3-2 nm,分散在LiXNUMXO中心。
為了證明電化學循環過程中磁性的變化,獲得了完全放電至 0.01 V 後的磁化曲線(圖 1d),顯示了由於奈米顆粒形成而產生的超順磁性行為。
圖1(a)在100 mAg−1Fe電流密度下循環的3O4/鋰電池的恆定電流充放電曲線; (b)全鋰Fe3O4電極的BF-STEM影像; (c) 聚集體中存在 Li2O 和 Fe 的高解析度 BF-STEM 影像; (d) Fe3O4電極之前(黑色)和之後(藍色)的磁滯曲線,以及後者(紫色)的朗之萬擬合曲線。
- 結構和磁演化的即時檢測
為了將電化學與 Fe3O4 的結構和磁性變化相結合,對電極進行了原位 X 射線衍射 (XRD) 和原位磁監測。 Fe在從開路電壓(OCV)到3V4O1.2的初始放電過程中的一系列XRD衍射圖中,衍射峰無論是強度或位置都沒有明顯變化(圖3a),顯示Fe4O2只經歷了Li嵌入過程。 當充電至3V時,Fe4O3的反尖晶石結構保持完整,顯示此電壓視窗內的過程是高度可逆的。 進一步進行原位磁監測與恆定電流充放電測試結合,以研究磁化強度如何即時演變(圖3b)。
圖2 原位X射線衍射和磁力監測表徵。(A)原位X射線衍射; (b) Fe3O4在3T外加磁場下的電化學充放電曲線及對應的可逆原位磁響應。
為了更基本地了解這種磁化強度變化的轉換過程,即時收集磁響應以及電化學驅動反應所伴隨的相應相變(圖 3)。 很明顯,在第一次放電期間,Fe3O4電極的磁化響應與其他循環不同,這是由於第一次鋰化過程中Fe3O4發生了不可逆相變。 當電位降至0.78V時,Fe3O4反尖晶石相轉變為含有Li2O的類FeO石鹽結構,Fe3O4相充電後無法恢復。 相應地,磁化強度迅速下降至0.482 μ b Fe−1。 隨著鋰化的進行,沒有新相形成,(200)和(220)類FeO衍射峰的強度開始減弱。等Fe3O4電極完全鋰化時沒有明顯的XRD峰保留(圖3a)。 注意到當Fe3O4電極從0.78V放電到0.45V時,磁化強度(從0.482μbFe−1增加到1.266μbFe−1),這歸因於從FeO到Fe的轉化反應。 然後,在放電結束時,磁化強度緩慢降低至1.132μB Fe−1。 這項發現表明,完全還原的金屬Fe0奈米粒子仍可能參與鋰儲存反應,從而降低電極的磁化強度。
圖3 相變和磁響應的原位觀察。(a)Fe3O4電極第一次放電過程中所擷取的原位XRD圖; (b) Fe3O4 在 3 T 外加磁場下對 / Li 電池電化學循環的原位磁力測量。
- Fe0/Li2O系的表面電容
Fe3O4電極的磁性變化發生在低電壓下,此時最有可能產生額外的電化學容量,這表明電池內存在未被發現的電荷載體。 為了探索潛在的儲鋰機制,透過XPS、STEM和磁性能譜研究了Fe3O4電極在0.01V、0.45V和1.4V處的磁化峰,以確定磁變化的來源。 結果表明,磁矩是影響磁變化的關鍵因素,因為測量的Fe0/Li2O系統的Ms不受磁性各向異性和粒間耦合的影響。
為了進一步了解Fe3O4電極在低電壓下的動力學特性,在不同的掃描速率下進行循環伏安法。 如圖4a所示,矩形循環伏安曲線出現在0.01V至1V的電壓範圍內(圖4a)。 圖 4b 顯示電極上發生 Fe3O4A 電容響應。 憑藉恆流充放電過程的高度可逆磁響應(圖4c),電極的磁化強度在放電過程中從1V下降到0.01V,並在充電過程中再次增加,顯示Fe0的類電容器表面反應是高度可逆的。
圖4 0.011 V下的電化學性能和原位磁表徵。(A)循環伏安曲線。(B)利用峰值電流和掃描速率之間的相關性確定b值; (c)在5T外加磁場下磁化強度相對於充放電曲線的可逆變化。
上述Fe3O4電極的電化學、結構和磁性特徵表明,額外的電池容量是由Fe0奈米粒子的自旋極化表面電容由伴隨的磁性變化引起的。 自旋極化電容是自旋極化電荷在界面累積的結果,在充電和放電過程中可以表現出磁響應。以Fe3O4為基電極,在第一次放電過程中,分散在O基底中的Li2細Fe奈米粒子具有由於高度局域化的 d 軌道,具有較大的表面積與體積比,並在費米能階實現高態密度。 根據邁爾的空間電荷儲存理論模型,作者提出,大量電子可以儲存在金屬 Fe 奈米顆粒的自旋分裂帶中,這可能會在 Fe / Li2O 奈米複合材料中創建自旋極化表面電容器(圖5 )。
圖5Fe/Li2A O界面處自旋極化電子的表面電容示意圖。(A)鐵磁金屬顆粒表面自旋極化態密度示意圖(放電前後),與鐵的體自旋極化; (b) 過量儲存的鋰的表面電容器模型中空間電荷區域的形成。
總結與展望
透過先進的原位磁監測研究了TM/Li2O奈米複合材料內部電子結構的演變,以揭示這種鋰離子電池額外儲存容量的來源。 結果表明,在 Fe3O4/Li 模型電池系統中,電化學還原的 Fe 奈米粒子可以儲存大量的自旋極化電子,這是由於電池容量過多和界面磁性顯著改變。 實驗進一步驗證了CoO、NiO、FeF2和Fe2N電極材料中此類電容的存在,顯示鋰離子電池中金屬奈米顆粒自旋極化表面電容的存在,並為此空間電荷儲存機制在其他躍遷中的應用奠定了基礎金屬化合物基電極材料。
文獻連結
原位磁力測量揭示過渡金屬氧化物鋰離子電池的額外儲存容量(Nature Materials,2020,DOI:10.1038/s41563-020-0756-y)
鋰電極晶片設計配方及電極晶片缺陷對性能的影響
- 極膜設計基礎篇
鋰電池電極是由顆粒組成的塗層,均勻地塗在金屬流體上。 鋰離子電池塗層可以看成是一種複合材料,主要由三個部分組成:
(1)活性物質顆粒;
(2)導電劑和助劑的構成相(碳黏合劑相);
(3) 孔隙,充滿電解液。
各相的體積關係表示為:
孔隙率+活物質體積分數+碳黏合劑相體積分數=1
鋰電池電極設計的設計非常重要,現在簡單介紹一下鋰電池電極設計的基礎。
(1) 電極材料的理論容量 電極材料的理論容量,即材料中所有鋰離子參與電化學反應所提供的容量,其值由下式計算:
例如,LiFePO4的摩爾質量為157.756 g/mol,其理論容量為:
此計算值僅為理論克容量。 為了確保材料的可逆結構,實際脫鋰係數小於1,材料的實際克容量為:
材料實際克容量=鋰離子拔出係數理論容量
(2)電池設計容量與極片密度電池設計容量可按下式計算:電池設計容量=塗層面密度活性物質比活性物質克容量極片塗層面積
其中,塗層的表面密度是關鍵的設計參數。 當壓實密度不變時,塗層面密度的增加意味著極片厚度增加,電子傳輸距離增加,電子電阻增加,但增加程度有限。 在厚電極片中,電解液中鋰離子遷移阻抗的增加是影響倍率特性的主要原因。 考慮到孔隙率和孔隙扭曲,孔隙中離子的遷移距離是極片厚度的許多倍。
(3)負正容量比N/P負容量與正容量之比定義為:
N/P應大於1.0,一般為1.04~1.20,這主要是在安全設計上,防止負極側鋰離子在沒有接受源的情況下析出,設計時要考慮製程容量,如鍍層偏差。 但當N/P過大時,電池會失去不可逆容量,導致電池容量低、電池能量密度降低。
對於鈦酸鋰負極,採用正極過剩設計,電池容量由鈦酸鋰負極的容量決定。 正極過剩設計有利於提高電池的高溫性能:高溫氣體主要來自負極。 在正極過剩設計中,負極電位較低,較容易在鈦酸鋰表面形成SEI膜。
(4) 塗層的壓實密度和孔隙率 在生產過程中,電池電極的塗層壓實密度按下式計算。 考慮極片滾壓時,金屬箔被拉伸,滾壓後塗層的表面密度按下式計算。
如前所述,塗層由活性物質相、碳黏合劑相和孔隙組成,孔隙率可以透過以下公式計算。
其中,塗層的平均密度為:鋰電池電極是一種粉末顆粒的塗層,由於粉末顆粒表面粗糙,形狀不規則,堆積時,顆粒與顆粒之間,有的顆粒本身就有裂縫和氣孔,所以粉體體積包括粉體體積、粉體顆粒與顆粒之間的孔隙,因此,對應各種焊條鍍層的密度和孔隙率的表示。 粉末顆粒的密度是指單位體積粉末的質量。 依粉末的體積分為真密度、顆粒密度、堆積密度三種。 各種密度定義如下:
- 真密度是指粉末質量除以不包括顆粒內部和外部間隙的體積(實際體積)而得到的密度。 即排除所有空隙的體積後所得到的物質本身的密度。
- 顆粒密度是指粉末質量除以包括開孔和閉孔的顆粒體積所得到的顆粒密度。 即顆粒間的間隙,而非顆粒內部的細孔,是顆粒本身的密度。
- 堆積密度,即塗層密度,是指粉末質量除以粉末形成的塗層的體積所得到的密度。 所使用的體積包括顆粒本身的孔和顆粒之間的空隙。
對於同一粉末,真密度>顆粒密度>堆積密度。 粉末的孔隙率是粉末顆粒塗層中孔隙的比例,即粉末顆粒之間的空隙和顆粒孔隙的體積與塗層總體積的比值,通常以百分比表示。 粉末的孔隙率是與顆粒形貌、表面狀態、粒徑和粒徑分佈有關的綜合性能。 其孔隙率直接影響電解液的滲透和鋰離子的傳輸。 一般來說,孔隙率越大,電解液越容易滲透,鋰離子傳輸越快。 因此,在鋰電池的設計中,有時要確定孔隙率,常用汞壓法、氣體吸附法等。也可以利用密度計算得到。 當使用不同的密度進行計算時,孔隙率也可能具有不同的意義。 當透過真密度計算生物體、導電劑和黏合劑的孔隙率的密度時,計算出的孔隙率包括顆粒之間的間隙和顆粒內部的間隙。 當透過顆粒密度計算活性物質、導電劑和黏合劑的孔隙率時,計算的孔隙率包括顆粒之間的間隙,但不包括顆粒內部的間隙。 因此,鋰電池電極片的孔徑也是多尺度的,一般顆粒之間的間隙為微米級尺寸,而顆粒內部的間隙為奈米至亞亞微米級尺寸。 在多孔電極中,有效擴散率和電導率等傳輸特性的關係可以用以下方程式表示:
其中D0表示材料本身的本徵擴散(傳導)速率,ε為對應相的體積分數,τ為對應相的迂迴曲率。 在宏觀均質模型中,一般採用Bruggeman關係式,取係數ɑ=1.5來估計多孔電極的有效正電性。
多孔電極的孔隙中填充有電解質,鋰離子在電解質中傳導,鋰離子的傳導特性與孔隙率密切相關。 孔隙率越大,電解質相的體積分數越高,鋰離子的有效電導率越大。 在正極片中,電子是透過碳黏結相傳輸的,碳黏結相的體積分數和碳黏結相的繞行直接決定了電子的有效導電率。
孔隙率和碳黏結相的體積分數是矛盾的,而孔隙率大必然導致碳黏結相的體積分數,因此,鋰離子和電子的有效傳導性能也是矛盾的,如圖2所示隨著孔隙率降低,鋰離子有效電導率降低,而電子有效電導率增加。 如何平衡兩者在電極設計中也至關重要。
圖2 孔隙率與鋰離子和電子電導率示意圖
2、電桿缺陷的類型及檢測
目前,在電池極柱製備過程中,越來越多地採用線上檢測技術,從而有效識別產品的製造缺陷,剔除不良品,並及時回饋到生產線,自動或手動調整生產工序,降低不良率。
極片製造中常用的線上檢測技術包括漿料特性檢測、極片品質檢測、尺寸檢測等,例如:(1)線上黏度計直接安裝在塗料儲槽中,檢測流變性。即時了解漿料的特性,測試漿料的穩定性; (2)鍍膜過程中採用X射線或β射線,其測量精度高,但輻射大,設備價格高,維護麻煩; (3)採用雷射線上測厚技術測量極片厚度,測量精度可達±1. 0 μm,還可即時顯示測量厚度及厚度的變化趨勢,便於數據追溯與分析; (4)CCD視覺技術,即採用線陣CCD對被測物體進行掃描,對缺陷類別進行即時影像處理與分析,實現極片表面缺陷的無損線上檢測。
作為品質控制的工具,線上測試技術對於了解缺陷與電池性能之間的相關性也至關重要,從而確定半成品的合格/不合格標準。
後一部分簡要介紹了鋰離子電池表面缺陷檢測技術、紅外線熱成像技術的新方法以及這些不同缺陷與電化學性能之間的關係。請諮詢D. Mohanty Mohanty等人的深入研究。
(一)極片表面常見缺陷
圖3顯示了鋰離子電池電極表面常見的缺陷,左側為光學影像,右側則為熱像儀擷取的影像。
圖3 極片表面常見缺陷:(a、b)鼓包/骨材; (c、d)掉落材料/針孔; (e、f)金屬異物; (g、h)塗層不均勻
(A、b)凸起/聚集,如果漿料攪拌不均勻或塗佈速度不穩定,就會出現此類缺陷。 黏合劑和炭黑導電劑的聚集導致活性成分含量低,極性片重量輕。
(c、d)滴/針孔,這些缺陷區域沒有被塗覆,通常是由漿料中的氣泡產生的。 它們減少活性材料的量並使集電器暴露於電解質,從而降低電化學容量。
(E、f)金屬異物、設備和環境中引入的漿料或金屬異物,金屬異物會對鋰電池造成很大的危害。 大的金屬顆粒直接損傷隔膜,導致正負極之間短路,這是物理短路。 另外,當正極混入金屬異物時,充電後正極電位升高,金屬溶解,透過電解液擴散,然後沉澱在負極表面,最後擊穿隔膜,形成短路,這是化學溶解短路。 電池廠現場最常見的金屬異物有Fe、Cu、Zn、Al、Sn、SUS等。
(g、h)塗佈不均勻,如漿料攪拌不充分,顆粒細度大時容易出現條紋,造成塗佈不均勻,影響電池容量的一致性,甚至出現完全無塗層條紋,對容量和安全性有影響。
(2)極片表面缺陷檢測技術採用紅外線(IR)熱成像技術來檢測乾電極上可能損害鋰離子電池性能的微小缺陷。 在線上檢測過程中,如果檢測到電極缺陷或污染物,在極片上進行標記,在後續工序中消除,並反饋到生產線,及時調整工藝,消除缺陷。 紅外線是一種電磁波,與無線電波和可見光具有相同的性質。 利用特殊的電子裝置將物體表面的溫度分佈轉換成人眼可見的影像,並以不同顏色顯示物體表面的溫度分佈,稱為紅外線熱成像技術。 這種電子設備稱為紅外線熱像儀。 所有高於絕對零度(-273℃)的物體都會發射紅外線輻射。
如圖4所示,紅外線熱近似儀(IR Camera)利用紅外線偵測器和光學成像物鏡接受被測目標物體的紅外線輻射能量分佈圖案,並將其反射到紅外線偵測器的光敏元件上,獲得紅外線熱影像,對應物體表面的熱分佈場。 當物體表面有缺陷時,該區域的溫度就會改變。 因此,該技術也可用於檢測物體表面的缺陷,特別適用於一些光學檢測手段無法區分的缺陷。 在線上檢測鋰離子電池乾燥電極時,電極電極首先受到閃光照射,表面溫度變化,然後用熱像儀檢測表面溫度。 熱分佈影像可視化,對影像進行即時處理分析,及時檢測表面缺陷並進行標記。 Mohanty研究在塗佈機乾燥箱出口處安裝了熱像儀,用於檢測電極片表面的溫度分佈影像。
圖5(a)是熱像儀偵測到的NMC正極片塗層表面的溫度分佈圖,其中含有肉眼無法辨別的極小缺陷。 內部插圖中顯示了與路線段相對應的溫度分佈曲線,在缺陷點處有溫度峰值。 在圖5(b)中,相應方框內溫度局部升高,與極片表面缺陷相對應。 圖. 圖6是表示有缺陷的負極片的表面溫度分佈圖,溫度上升的峰值對應於氣泡或聚集體,溫度下降的面積對應於針孔或液滴。
圖5 正極片表面溫度分佈
圖6 負極表面溫度分佈
可見,溫度分佈熱成像檢測是極片表面缺陷檢測的良好手段,可用於極片製造的品質控制。3. 極片表面缺陷對電池性能的影響
(1)對電池倍增容量及庫倫效率的影響
圖7為骨材和針孔對電池倍增容量和庫倫效率的影響曲線。 聚集體實際上可以提高電池容量,但會降低庫倫效率。 針孔降低了電池容量和庫倫效率,高倍率時庫倫效率下降很大。
圖7 正極聚集體和針孔對電池容量和效率的影響圖8是鍍層不均勻、金屬異物Co和Al對電池容量和效率的影響曲線,鍍層不均勻降低電池單位質量容量10%—— 20% ,但整個電池容量下降了60%,這表明極片中的活體質量明顯減少。 金屬Co異物降低了容量和庫侖效率,即使在2C和5C高倍下,也完全沒有容量,這可能是由於鋰和鋰嵌入的電化學反應中形成金屬Co,也可能是金屬顆粒堵塞隔膜孔造成微短路。
圖8 正極塗層不均勻和金屬異物Co、Al對電池倍增容量和庫倫效率的影響
正極片缺陷總結:正極片塗層中的鹽降低了電池的庫侖效率。 正極塗層的針孔降低了庫侖效率,導致倍增器性能較差,尤其是在高電流密度下。 異質塗層的放大性能較差。 金屬顆粒污染物可能會導致微短路,從而可能大大降低電池容量。
圖9顯示了負極漏箔條對電池倍增容量和庫倫效率的影響。 當負極發生漏液時,電池的容量明顯降低,但克容量不明顯,對庫倫效率的影響並不顯著。
圖9 負極漏箔剝離對電池倍增容量和庫倫效率的影響 (2) 對電池倍增循環性能的影響 圖10是電極表面缺陷對電池倍增循環的影響結果。 影響結果摘要如下:
平均:2C循環時,200次循環容量維持率為70%,不良電池為12%;5C循環時,200次循環容量維持率為50%,不良電池為14%。
針孔:容量衰減明顯,但無聚集體缺陷衰減快,200次循環2C和5C容量維持率分別為47%和40%。
金屬異物:金屬Co異物經過幾次循環後容量幾乎為0,金屬異物Al箔5C循環容量明顯下降。
漏電條:對於相同的漏電面積,多個較小條帶的電池容量比大條帶下降得更快(47C 200 次循環為 5%)(7C 200 次循環為 5%)。 這表示條紋數量越多,對電池循環的影響越大。
圖10 電極片表面缺陷對電池倍率循環的影響
參考文獻: [1] 線上雷射測徑儀與紅外線熱成像方法對槽模塗層鋰二次電池電極的無損評估[J].ANALYTICALMETHODS.2014, 6(3): 674-683.[2]效果王偉, etc. 電極製造缺陷對鋰離子電池電化學性能的影響:電池失效源的認識[J]. 電源學報.2016, 312: 70-79.
上一篇: 歐洲電池產業:十年衰退與復興之路
下一個: 歐洲電池產業:十年衰退與復興之路